TM 5-3895-374-24-2
32.
Limit control check should be made as follows:
A)
Permit the burner to run until the limit control
settings have been reached.
B)
The burner should turn off when the set
temperature or pressure has been reached. If the
burner is Low/High/Low or Modulating, set the
controls so that the burner will go to the low fire
position before the operating limit control turns the
burner off.
C)
After the differential pressure or temperature
drop, the burner should start automatically.
D)
With the unit running normally, open the blow-
down valve and remove water to the point below
the low water cutoff setting. The burner should
turn off and restart automatically when the proper
water level is re-established. (If manual reset
type low water cutoff is used, it will have to be
reset.)
E)
Set and check operation of:
(1)
Low Oil Pressure Switch (if supplied). Set
at 80% of low fire oil pressure. Check
visually, or test electrically to confirm that
circuit opens at the proper oil pressure.
(2)
Blower Combustion Air Flow Switch (if
supplied).
(a)
Shut burner power off.
(b)
Disconnect both wires at the air flow
switch and temporarily clip them together.
Make sure that they cannot ground
against anything, since they will be
powered with 110 Volts during the test.
(c)
Put a continuity meter across the two
terminals.
(d)
Disconnect
the
wire
to
the
main
automatic oil valve.
(e)
Start the blower motor. The meter should
read electrical continuity as soon as the
blower starts.
(f)
Disconnect the blower motor lead wire, or
open the main power disconnect switch
to
the burner. Within 4 to 5 seconds after
the blower motor is de-energized, the
meter should indicate an open air flow
switch circuit (no continuity).
(g)
If the switch does not open in 4 to 5
seconds, readjust accordingly. Turn the
air
flow
switch
adjustment
screw
clockwise to shorten cut-off response
time, and counter-clockwise to lengthen
cut-off response time.
(h)
Turn the burner power off. Remove the
shorting clip from the two disconnected
wires and let them hang loose. (They will
be powered with 110 Volts, so do not let
them ground out.)
(i)
Reconnect the wire to the main automatic
oil valve. Turn the burner on. With the air
flow
switch
wires
disconnected,
the
burner should go into a purge cycle, but
neither the ignition nor the main fuel valve
circuits will be energized. If they do
energize, there is a wiring problem.
Correct as required.
(j)
Turn power off. Reconnect the air flow
switch wires to the air flow switch
terminals. Place burner back into normal
operation.
(3)
All burner and heat exchanger controls
and operating devices.
33.
The Owner's Operating Instructions, page 43 of this
manual, should be posted in a clearly visible location
close to the burner.
34.
If the burner operation is abnormal, refer to Section 7
Trouble Shooting Suggestions, as well as trouble
shooting
information
in
the
flame
safeguard
manufacturer's bulletin shipped with the burner. It is also
strongly suggested that all test procedures outlined in the
flame safeguard control manufacturer's bulletin be
conducted.
35.
Complete the Burner Start Up Information and Test
Data sheets on pages 41 and 42.
7 SERVICING AND COMPONENT ADJUSTMENTS
General Information on Internal Bypass Oil Nozzle Systems
1.
The system is designed to use 300 PSI pressure at the
nozzle inlet at low and high fire (and throughout the
range on modulating systems). The firing rate is
changed by an adjustable bypass arrangement that
allows more or less oil to bypass the nozzle and flow to
the return line. Low fire pressures at the bypass
pressure test tee will generally be from 60 to 100 PSI,
with high fire bypass pressures from 180 to 225 PSI.
These pressures will vary depending upon the nozzle
size selection and specific job firing conditions. See
page 30, Table 8 for flow rates, sizing and pressure
information.
2.
Smoky fires with apparent large droplet size in the spray
pattern are generally caused by low nozzle or return flow
pressures. To properly check the system, it is necessary
to verify both nozzle supply and return pressures. Also
check to make certain that the nozzle adapter and
strainer are not partially plugged.
3.
Careless cleaning or handling of the nozzle may damage
the orifice, causing heavy streaks in the oil
spray. This will also show up as large droplets or sparks
in the flame.
4.
Off center fires, low bypass line pressures and safety
lockouts (due to poor spray pattern and ignition failure)
may result from plugged slots in the nozzle distributor
head. When such situations are observed, the nozzle
should be removed, disassembled and cleaned.
5.
Excessive after squirt of oil is caused by air in the
system. Be sure air is not trapped in pressure gauges,
overhead oil lines or fittings. A leaking check valve on
the bypass return line from the nozzle can create the
same effect.
6.
The Teflon seal should stay on the nozzle when
servicing. On some sizes of burners using Delavan
30630 and 30637 Series nozzles, the Teflon seal stays in
the nozzle adapter. If it is damaged through careless
handling, the resulting leak will cause an increase in the
burning rate, when the bypass line is closed at high fire.
(page 3 - 981)
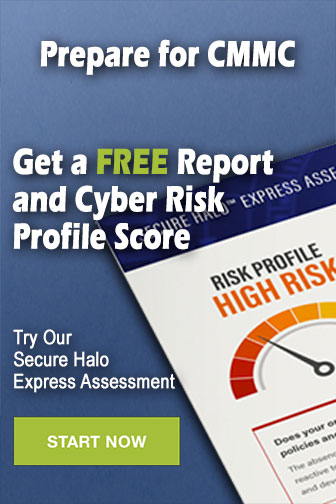