TM 5-3895-374-24-2
17.
For Low/High/Off burners · adjust the main gas pressure
regulator in combination with the air damper linkage
operation to achieve 8 1/2 to 10% CO2 and 0% CO at the
full high fire input rate position. Make certain the linkage
operates smoothly and without binding or overtravel of
the air damper stops.
18.
For Low/High/Low burners - adjust the main gas
pressure regulator in combination with the air damper
linkage operation to achieve 81 to 10% CO2 and 0% CO
at the full high fire input rate position. Make certain the
linkage operates
of the air damper stops. Run burner to the low fire
position and lock motorized gas valve internal low fire
adjustment to a setting that will attain 7 to 9% CO2 and
0% CO at the desired low fire input rate.
19.
Intermittently operate the burner until the water is warm
in
the
boiler,
or
follow
specific
initial
firing
recommendations provided by the heat exchanger
manufacturer.
20.
See items 31 through 35 in this section for recommended
limit control and other control devices operational
checkout.
Burners Designed for Full Modulation Operation
After completing pilot adjustments and other procedures as
appropriate in items 1 through 15 above, proceed with modulating
adjustments as follows:
21.
Initial adjustments should be made at the low fire
position. All Power Flame burners are factory tested and
adjusted. However, to determine that the metering
butterfly valve is, in fact, in the low fire position, observe
the end of the metering valve shaft. The slot in the end
of the shaft indicates the position of the valve. When the
slot is in the horizontal position (parallel with the gas flow
direction), the valve is fully open. Refer to page 21, Fig.
28 for linkage adjustment information and page 20, Fig.
27 for adjustment information on the VaricamTM
characterized fuel metering system.
22.
Turn the burner on and let it advance to the main flame
light off position. Take action as necessary to hold the
linkage at the low fire position by using a manual
potentiometer
or
electrically
disconnecting
the
modulating motor. Power Flame burners are tested at
the factory and linkage adjustments for modulation are
made at that time. Note that the factory settings relate to
good operation while firing into open test pits, and
therefore will normally not relate directly to absolute
fuel/air ratios while firing under specific field conditions.
It is suggested that the factory settings be noted and
marked on the linkage prior to proceeding with final
adjustment. In this manner those settings can be
restored as initial reference points, if need be.
23.
With the burner in the factory set low fire position,
adjust air and fuel linkage to good fuel/air ratio low fire
settings (7 - 9% CO2, 0% CO). Mark the linkage at the
new settings.
24.
Increase the firing rate to the midway point. Set the
fuel/air ratios to achieve good combustion values (7 - 9%
CO2, 0% CO). Mark the linkage as a reference point for
this new mid fire position.
25.
Increase the rate to high fire position and repeat the test
done for the mid point adjustment. Results should range
in the area of 81 to 10% CO2, with 0% CO. The
metering device setting and air damper openings should
be marked and noted to obtain high fire reference points.
It should be noted that an additional point of the fire
adjustment may be smoothly and without binding or
overtravel
obtained by modifying the regulated gas pressure
delivered to the burner metering device. The burner
pressure regulator is used to obtain this adjustment and
can be used within available pressure limits to obtain
optimum firing conditions.
26.
Operate the modulating lever arm on the modulating
motor through the three previously referenced points.
Minor setting modifications may be required to ensure
that the reference points are acquired.
27.
Tighten (finger tight) the hex bolt to the linkage rod at the
swivel on the modulating motor driver arms and run the
motor through its full travel to ensure that the linkage is
free and that limits on the metering device and air
dampers are not exceeded. 28. Determine that the
required gas input rate is being achieved by clocking the
gas flow at the gas meter. The gas utility should be
consulted to determine if any correction factors have to
be applied to the indicated meter flow rates. Refer to
page 36 for additional combustion analysis information
and to page 6 for additional firing rate information.
29.
Intermittently operate the burner until the water is warm
in
the
boiler,
or
follow
specific
initial
firing
recommendations provided by the heat exchanger
manufacturer.
30.
Tighten all linkages and permanently mark settings.
31.
Limit control check should be made as follows:
A)
Permit the burner to run until the limit control
settings have been reached.
B)
The burner should turn off when the set
temperature or pressure has been reached. If the
burner is Low/High/Low or Modulating, set the
controls so that the burner will go to the low fire
position before the operating limit control turns the
burner off.
C)
After a differential pressure or temperature drop,
the burner should restart automatically.
D)
With the unit running normally, open the blow
down valve and remove water to the point below
the Low Water Cut Off Setting. The burner
should turn off and restart automatically when the
proper water level is re-established. (If manual
reset type LWCO is used, it will have to be reset.)
(page 3 - 977)
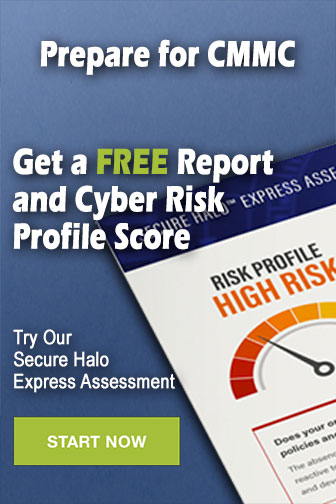