TM 5-3895-374-24-2
Table 9
OIL NOZZLE FLOW RATE CHARTS
Simplex Nozzle System (Monarch PLP or Equivalent Solid or Semi Solid)
Flow Rate vs Pressure
Capacity in GPH #2 Oil
100#
Nominal
Rating
120#
140#
160#
180#
200#
240#
260#
280#
300#
2
2.1
2.3
2.4
2.6
2.7
3.0
3.1
3.2
3.3
2.5
2.6
2.8
3.0
3.2
3.4
3.7
3.8
4.0
4.1
3
3.2
3.4
3.6
3.8
4.0
4.4
4.7
4.8
5.0
3.5
3.7
3.9
4.2
4.5
4.7
4.2
5.4
5.8
5.9
4
4.2
4.5
4.8
5.1
5.4
5.9
6.2
6.4
6.7
4.5
4.7
5.0
5.4
5.7
6.1
6.6
7.0
7.2
7.4
5
5.3
5.6
6.0
6.4
6.8
7.3
7.7
7.9
8.2
5.5
5.7
6.1
6.5
7.0
7.3
8.0
8.4
8.6
9.1
6
6.3
6.7
7.2
7.7
8.1
8.8
9.2
9.5
9.9
6.5
6.8
7.2
7.9
8.3
8.8
9.5
10.0
10.3
10.7
7
7.3
7.9
8.3
9.0
9.4
10.3
10.7
11.2
11.4
7.5
7.8
8.5
8.9
9.6
10.0
11.0
11.5
11.9
12.2
8
8.3
9.1
9.5
10.3
10.8
11.8
12.3
12.8
13.0
9
9.4
10.1
10.8
11.5
12.0
13.2
13.9
14.4
14.8
10
10.4
11.2
12.0
12.8
13.4
14.7
15.4
16.0
16.6
11
11.5
12.5
13.3
14.2
15.0
16.2
17.0
17.7
18.2
12
12.5
13.6
14.5
15.3
16.2
17.7
18.5
19.2
19.8
Oil Nozzle Servicing
1.
Nozzles used on Power Flame Type C burners are of two
types: simplex and internal bypass. The simplex nozzle
is normally used on smaller burners in the three to eight
gallons per hour range. The bypass nozzle is used for
larger
inputs
requiring
higher
turndown
or
more
sophisticated air/fuel control. Both types of nozzles have
GPH ratings stamped on the side. Stamped ratings are
based on 100 psig. The burners operate in the 300 psig
range. See pages 30 and 31, Tables 8 and 9 for flow
rates, pressure and sizing information.
2.
When removing or replacing the oil nozzle and electrode
assembly, take care to prevent damage to the ignition
wire.
3.
The nozzles should be removed from the nozzle adapter
by use of the proper wrench. They should be
disassembled and thoroughly cleaned with a liquid
solvent (preferably non-flammable) and a brush.
4.
Do not use a screwdriver, wire brush or similar metallic
objects to clean nozzles. Damage to orifices or spray
slots result in off-center or sparky fires.
5.
The nozzle should be seated firmly in the nozzle adapter
to prevent leaks.
6.
If a nozzle is damaged or burned, replace it.
7.
The entire oil tube and nozzle assembly (the oil drawer
assembly) may be removed for ease of service.
8.
When cleaning and taking the nozzle apart, do not force
it.
9.
For additional information on bypass nozzles, see page
30. Note that the Teflon seal in the Monarch F80BPS
and Delavan 33769 nozzles is an integral part of the
nozzles and that if the seal is removed accidentally, the
nozzle must be replaced. On the Delavan 30630 and
30637 nozzles, the seal normally remains in the nozzle
adapter. When the nozzle is removed from the adapter,
the seal should also be removed and replaced with a new
seal.
Oil Pump or Oil Flow Problems and Typical Solutions
NO OIL DELIVERED
1. Reversed pump rotation
2. Suction lift too high (See page 10, Fig. 10)
3. Air leak in suction line
4. Pump not primed, or has lost prime
5. Pump coupling not installed properly
6. Pump defective
7. Line plugged
8. Valve closed
CAPACITY TOO LOW
1. Suction lift too high (See page 10, Fig. 10)
2. Air leak in suction line
3. Suction line too small (See page 10, Fig. 10)
4. Check valve or strainer is obstructed or dirty
5. Mechanical defects pump badly worn or seal defective
NOISY PUMP
1. Air leak in suction line
2. Pump not securely mounted
3. Vibration caused by bent shaft or misalignment
4. Pump overloaded
5. Suction line vacuum so high that vapor forms within the liquid
(see page 10, Fig. 10)
PUMP LEAKS
1. Cover bolts need tightening; gasket broken or defective
2. Mechanical seal (used on certain models) may be scratched,
due to dirt
3. Inlet head pressure too high. Install a pressure reducing valve
set at 3 psig or less.
4. Oil line fittings not tight For additional oil pump information,
refer to the oil pump manufacturer's product bulletin supplied
with the burner.
(page 3-983)
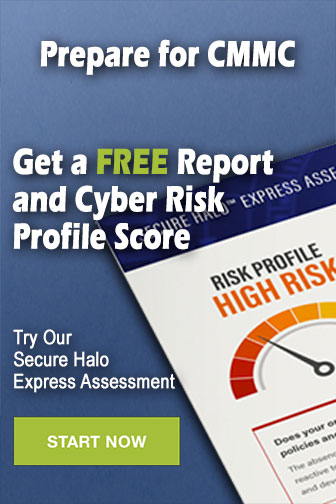