TM 5-3895-374-24-2
Burner Start Up Sequence Instructions
1.
Prior to burner start up - contact the local gas company
to determine if any correction factors have to be applied
to their indicated meter flow rates. This information is
important as relates to achieving specific heat exchanger
BTU/HR inputs. Refer to page 36 for additional
combustion analysis information and to page 6 for firing
rate information.
2.
Refer to the gas piping diagram furnished with the
burner. Check gas piping, controls and valves for leaks
and compliance with codes.
3.
Check all linkages. If the system is a packaged
burner/heat exchanger system, the linkage was probably
set when the system was test fired at the heat exchanger
manufacturers factory. It should, however, be checked
to ensure that it was not damaged in shipment. On
conversion units (where the burner and heat exchanger
are mated in the field), the linkage will have to be set to
suit the particular operating conditions.
4.
Do not secure flame safeguard control into its wiring
base until it has been determined that there are no shorts
or grounds in the system.
5.
Remove the pilot assembly and check for proper settings
of the spark gap, tightness of electrode in its bracket and
firm connections of the electrode cable. (See Page 35.)
6.
Close main, checking and pilot gas cocks. Install one
gas pressure gauge to read burner firing head pressure
(use a 0-10 W.C. gauge or a manometer). See Section
3 for pressure sensing locations. Install a second gas
pressure gauge to read gas supply pressure between the
main gas cock and the inlet to the main gas pressure
regulator (use a 0-35 W.C. gauge or as appropriate). If
there is no tapping in this location, install a tee at the
point where the pilot gas supply is connected to the main
gas line. Slowly open the main gas cock in order to
determine that the incoming gas pressure is within the
specified limits of the main and pilot gas pressure
regulators, automatic fuel valves and gas pressure
switches. Many systems are rated for a maximum gas
supply of pressure of 14 W.C. If pressure exceeds this
value, consult the first page of the Burner Specification
Sheet and/or gas component product bulletins supplied
with the burner to ensure that the supplied system can
operate properly at such elevated supply pressure.
7.
Disconnect pilot line at inlet to the pilot gas pressure
regulator and purge air from the pilot gas line. Purging of
gas lines must be done in accordance with NFPA 54 of
the National Fire Protection Association's National Fuel
Gas Code. After the air is purged from the gas supply
system, close the pilot cock and reconnect the pilot line.
Leave the pilot cock closed.
8.
Install required system measuring devices: a) appropriate
flame signal meter to the flame safeguard control; b)
manometer (or 0-10 W.C. gauge) in the pilot test tee
port; c) stack thermometer and CO2 or O2 sample line to
the breaching; and d) draft gauge to the combustion
chamber test point.
9.
It is strongly recommended that an automatic gas valve
bubble leak test be performed in accordance with the
gas valve manufacturer's instructions on every new
installation and periodically afterwards in order to ensure
that the valve is functioning according to the
manufacturers specifications.
according to the manufacturer's specifications. It is also
suggested that the test be conducted during a normal
prepurge burner operation. This test will reveal any
problems that relate to incorrect wiring of the automatic
gas valve that could cause premature energization of the
valve.
10.
Set the air dampers approximately 1/4 open, and with
both pilot and leak test gas cocks closed, open the main
gas cock (to allow the low gas pressure switch, if
supplied, to make its circuit). With the control switch in
the Off position, apply power to the burner through the
main burner disconnect switch. Switch the burner panel
On/Off switch to the On position momentarily to
determine that the blower rotation is correct.
11.
Restart the burner. With the pilot gas cock closed, the
burner will go through a blower prepurge period, after
which the gas pilot ignition transformer will be energized,
although no pilot will be established. (At no time should
there be any flame signal reading, nor should the main
gas valve attempt to open.) At the end of the pilot trial for
ignition and blower purge period, the flame safeguard
control should shut the system down in a safety lock-out
mode, requiring manual reset of the flame safeguard
control to restart the burner.
12.
Wait three minutes, reset the flame safeguard control
safety switch (restarting the burner) and open the pilot
gas cock. When the blower prepurge period ends and
the burner is energized - if the flame safeguard control
has a time stop/run switch - stop the timer while the
pilot is on and make adjustments as required. See page
34 for pilot ignition adjustments. If the burner has
automatic air damper operation (dampers moved by the
automatic gas valve or modulating motor) and the Flame
Safeguard control does not have a timer stop/run
switch, it will be necessary to keep the air dampers in the
pilot light off (low air flow) position by temporarily
electrically disconnecting the motorized gas valve or
modulating motor to complete pilot adjustments. Recycle
the burner several times to make certain pilot operation
is reliable.
13.
With pilot adjustments completed, reset the timer switch
to the Run position, which will allow the sequence to
proceed to the automatic gas valve energizing position.
If the motorized gas valve or modulating motor wires
have been disconnected, shut the burner off and
reconnect electrically to allow normal automatic air
damper operation.
14.
When the main automatic gas valve begins to open,
slowly open the checking gas cock to light off the main
flame. The main flame should light immediately. If not, it
may be necessary to eliminate air from the main gas line
and/or adjust main gas pressure regulator flow rates.
15.
Adjust the burner as necessary to provide smooth
ignition of the main flame. If the flame signal drops
significantly when the main automatic gas valve opens,
slightly increase the pilot gas pressure to attain a stable
flame signal value.
16.
For On/Off burners - adjust the main gas pressure
regulator to achieve the proper main flame gas input.
Set and lock the air dampers to provide 8 1/2 to 10%
CO2 (Carbon Dioxide) and 0% CO (Carbon Monoxide).
Make certain the gas pilot operates reliably at the final
fuel/air settings.
(page 3 - 976)
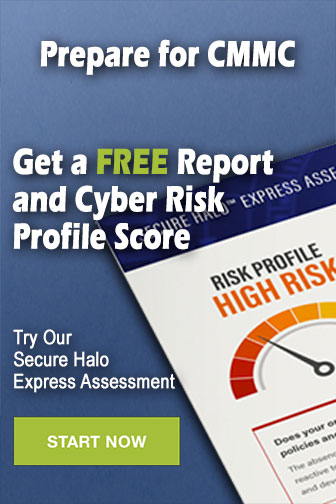