TM 5-3895-374-24-2
Step 8.
LOW OIL LEVEL SWITCH
A float activated switch is installed to protect your
compressor
against damage due to insufficient oil level.
The
switch
operates
on
a
fail-safe
principle
and
is
mechanically actuated for sealed, friction-less operation. Low
oil level in the frames causes the switch contacts to open, thus
shutting the unit down until the proper oil level has been
restored.
The Low Oil Level Switch is a single pole, double
throw snap
switch, available with a NEMA 1 enclosure.
(An optional NEMA 7 enclosure is available). (See Wiring
Diagram on Page 24 for connection of the Low Oil Level
Switch.)
NEMA 1 ENCLOSURE: This switch has a maximum
rating of 5 amps at 125,250 or 480 volt operation and uses a
%" nominal size flexible steel conduit, of a length as required,
over the switch lead wires. The switch is not acceptable for
greater than 480 volts.
(Optional) NEMA 7 ENCLOSURE: This switch has a
maximum rating of 4 amps at 250 volt operation and is
equipped with a 2 1/2" NPT non-removable fitting.
WARNING
Proper protection against low oil levels depends on
proper
adjustment of the low oil level switch.
During the initial run, stop unit and drain one quart of
oil from crankcase into clean can, and listen for switch to click
or check with continuity tester.
This is a "float" type switch which sometimes gets
cocked in shipping. If cocked or stuck, open disconnect
switch, drain remaining oil, remove crankcase cover and then
free the float. Reassemble and then reuse the same oil.
NOTE
If float is cocked in the low position,
compressor cannot start.
Step 9
DISCHARGE PIPING
The following general instructions cover only the
installation of discharge piping and placement of safety valves,
pressure switch, pressure gauge, auxiliary valve, drain valves,
shut-off valves, etc. in systems using a detached receiver.
See Figure 2-3. Discharge piping should be the same size as
the
compressor
discharge
connection
or
the
receiver
discharge connection( All
pipe and fittings must be certified safe for the pressures
involved. Pipe thread sealant is to be used on all threads, and
all joints are to be made up tightly, since small leaks in the
discharge system are the largest single cause of high
operating costs. If your compressor runs more than you
believe it should, the most likely cause is a leaky pipe line.
Leaks are easily located by squirting soap and water solution
around the joints and watching for bubbles.
When
a
baseplate
mounted
unit
or
a
bare
compressor is supplied, it is very important to observe the
following points when installing the piping between the
compressor and the receiver.
WARNING
1.
If possible, run the piping down from the compressor
discharge to permit the condensate to drain into the
receiver. If this is not possible, Install a "drain leg" as
shown in Figure 2-3. The drain leg should project
down from the compressor discharge and be at least
10" (254 mm) long.
2.
Put a drain valve at the end of this pipe and drain at
least weekly, or as often as necessary.
Figure 2-3. Typical piping arrangement for compressor and
detached receiver.
The length of the tube line connecting the auxiliary
valve will have a bearing on the operation of the regulation
system. For lengths up to 12 feet (3.6 m), use 5/16 O.D.
copper tubing that has been certified safe for the pressures
involved. For lengths over 12 feet (3.6 m), use the next larger
size copper tubing that is certified safe for pressures involved,
or contact your nearest I-R distributor.
Step 10.
COMPLETE WARRANTY REGISTRATION
Completion
of
the
registration
form
indicates
satisfactory
installation
and
performance
of
start-up
operations. If any defects are apparent in the equipment;
contact the nearest I-R Distributor or Ingersoll-Rand District
office. The I-R service literature included with the unit has
instructions for minor adjustments. Minor adjustments are not
considered warranty.
page 3-833
Hazardous voltage.
Connecting pressure switch or low oil level
switch directly to motor can cause severe
injury or death.
Always insure the pressure switch or low oil
level switch is connected thru the control
circuit of a magnetic starter.
This machine contains high pressure air. Can
cause eye injury or death from flying parts.
If an after cooler, check valve, block valve or
any
other
restriction
is
added
to
the
compressor discharge and ASME approved
safety valve must be installed between the
compressor discharge and the restriction.
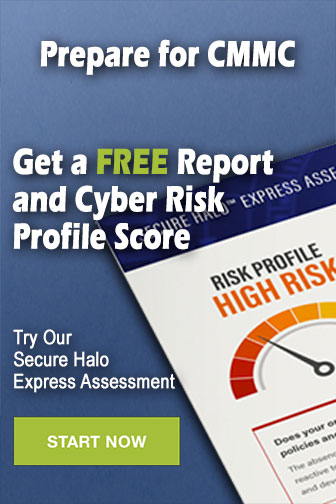