TM 5-3895-374-24-2
Table 2-Recommended Oil Grades.
Ambient
Viscosity Range
Approx.
Approx.
Temperature F
SSU at 100 F.
SAE No.
ISO No.
(C)
(38C)
Above 90 (32)
1000-1200
50
320
32 to 90 (0 to 32)
700-1000
40
220
0 to 32 (-18 to 0)
500-700
30
150
Below 0 (-18)
300-500
20
100
To fill the gearbox, remove the breather plug and the
oil overflow plug (Fig. 3). Fill the reservoir up to the
overflow hole. Place the breather and the overflow plug
back into their respective holes.
Table 3-Oil Sump Capacities.
Frame
Capacity, Fl. Oz. (Liters)
Size
Vertical
Horizontal
22
3.4 (.1)
6.1(.18)
24
3.4 (.1)
6.11(.18
32
8.5 (.25)
16.0 I(.47)
33
8.5 1(.25)
16.0 I(.47)
36
8.5 1(.25)
16.0 1(.47)
42
12.7 1(.37)
22.8 (.67)
45
12.7 1(.37) 1
22.8 1(.67)
47
12.7 1(.37)
22.8 (.67)
53
16.0 1(.47)
27.6 1(.82)
56
16.0 1(.47)
27.6 (.82)
59
16.0 1(.47)
27.6 1(.82)
65
28.3 1(.84)
52.1 (1.54)
68
28.3 1(.84)
52.1 11(.54)
615
28.3 (.84) i
52.1 )1(.54)
76
32.3 (.96)
59.5 11(.76)
711 l
32.3 (.96)
59.5 11(.76)
718
32.3 (.96)
59.5 11.76)
Proper lubrication is usually the most important
single consideration in obtaining maximum service life
and the most satisfactory operation from the unit. Unless
operating conditions are quite severe, a weekly check of
gearhouse oil level and necessary addition of lubricant
should be sufficient. However, oil should be changed
after initial 100 hours of operation. Thereafter, a
complete oil change normally is made after 1000
operating hours, or less, depending on the type of oil and
oil operating temperature.
Shaft bearings at the drive end of the blower are
grease lubricated and each bearing housing is equipped
with pressure type grease fittings and pressure type relief
fittings. When servicing drive end bearings, use a NLGI
#2 premium grade, petroleum base grease with high
temperature (300° service temperature) and moisture
resistance and good mechanical stability. Using a
pressure gun, force new lubricant into each drive end
bearing housing until traces of clean grease comes out
of the relief fitting.
After a long shutdown, it is recommended that the
grease relief fittings be removed, the old grease flushed
out with kerosene or #10 lubricating oil, drained
thoroughly, and bearings refilled with new grease. Be
sure grease relief fittings are reinstalled. Grease should
be added using hand operated grease gun to the drive
end bearings at varying time intervals depending on duty
cycle and RPM. Table 4 has been prepared as a general
greasing schedule guide based on average operating
conditions. More frequent intervals may be necessary
depending on the grease operating temperature and
under unusual circumstances.
Table 4-Suggested Bearing
Lubrication Intervals.
Speed
Operating Hours Per Day
in
8
16
24
RPM
Greasing Intervals in Weeks
750-1000
7
4
2
1000-1500
5
2
1
1500-2000
4
2
1
2000-2500
3
1
1
2500-3000
2
1
1
3000 and up
1
1
1
OPERATION
Before operating a blower under power for the first
time, check the unit and the installation thoroughly to
reduce the likelihood of avoidable troubles. Use the
following procedure list as a guide, but consider any
other special conditions in the installation.
1.
Be certain that no bolts, tools, rags or dirt have been
left in the blower air chamber.
2.
Be certain that inlet piping is free of debris. If an
outdoor intake without filter is used, be sure the
opening is located so it cannot pick up dirt and is
protected by a strong screen or grille. Use of the
temporary protective screen at the blower as
described
under
INSTALLATION
is
strongly
recommended.
3.
Recheck blower leveling, drive alignment and
tightness of all mounting bolts if installation is not
recent. If belt drive is used, adjust belt tension
correctly.
4.
Turn drive shaft by hand to make sure impellers still
rotate without bumping or rubbing at any point.
5.
Make sure oil level in blower gearbox is correct.
6.
Check lubrication of driver. If it is an electric motor,
be sure that power is available and that electrical
overload devices are installed and workable.
7.
Open the manual unloading valve in the discharge
air line. If a valve is in the inlet piping, be sure it is
open.
8.
Bump blower a few revolutions with driver to check
that direction of rotation is correct, and that both
units coast freely to a stop.
After the preceding points are cleared, blower is
ready for trial operation under "no-load" conditions as set
up under Item 7. The following procedure is suggested
to cover this initial operating test period.
a.
Start blower, let it accelerate to full speed, then shut
off. Listen for knocking sounds, both with power on
and as speed slows down.
b.
Repeat above, but let blower run 2 or 3 minutes.
Check for noises, and vibrations of 5 mils or greater.
c.
Operate blower for about 10 minutes unloaded.
Check oil levels. Feel cylinder and headplate
surfaces for development of spots too hot to touch,
indicating impeller rubs. Be aware of any noticeable
increase in vibration.
Assuming that all trials have been satisfactory, or
that necessary corrections have been made, the blower
should now have a final check run of at least one hour
under normal operating conditions. After blower is
restarted
page 3-807
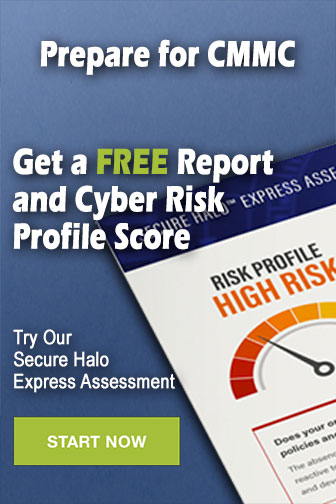