TM 5-3895-374-24-2
location as in original assembly. Before starting
the shafts through the headplate holes. make
sure shaft ends have no sharp or rough edges to
damage seal lips. Position impellers at 90° to
each other in the cylinder, using lobe-and-waist
match marks if original impellers are being re-
installed. Install drive end headplate and feet in
same manner as gear end.
10. It is recommended that new bearings be used
for rebuild. Apply thin film of machine oil on the
shaft bearing fit, bearing I.D., and headplate
bearing bore. Install drive end bearings into
headplate. Use a tube with flanged end that will
contact both bearing faces simultaneously.
Refer to Fig. 11 for proper bearing depths.
NOTE: Cylindrical drive bearing should be
installed with inner race large shoulder facing
outboard.
11. Place blower on its feet on a flat surface.
Loosen feet capscrews (32) and square up unit.
Re-tighten capscrews (32). Clamp unit down to
a solid base for further assembly.
12. Oil the gear end bearing fits as described
previously. Install 2 1/2-5" UNIVERSAL RAI
gear end bearings flush with the headplate
bearing shoulders using proper drivers. On 6" &
7" UNIVERSAL RAI®, install thrust washer (29)
in bearing bores then install gear end bearings
so that they protrude 1/16 (1.6mm) above
headplate surface.
13. Install bearing clamp plates (34). On 6" & 7"
UNIVERSAL RAI®, impeller end clearances are
also to be set during this step. Install clamp
plates (34) with capscrews (31) making sure that
the gap between the clamp plates and the
headplate is even all around, at the same time,
set end clearances per Table 5.
14. Install gears and time impellers as in (A).
15. For setting end clearances on 2 ½ - 5" gear
diameter units, special tools. thrust adjuster fork
Fig. 7 and thrust adjuster saddle Figure 8 are
required. Refer to Fig. 6 for installation of tools.
The flat side of the saddle rests against the
bearing inner race and the flat side of the fork
rests against the back side of the gear. Install a
shim, with thickness equal to gear end clearance
(Table 6), between the impeller and the gear end
headplates. Tap on top of the fork until the shim
becomes snug. Remove the shim and check
end clearances. To increase gear end
clearance, tap on the end of the gear end shaft
with
a soft metal mallet. On units, UNIVERSAL RAI.
set end clearances for 6" & 7 by turning
capscrews (31) evenly in or out.
16. Install drive end cover (5) after packing bearing
cavities with suitable grease. Replace drive
shaft seal. Lip must point toward (33) the
bearing. Exercise care not to damage the Lip as
it passes over shaft keyway.
17. Install gasket item (7). Install the gear house
after cleaning out the inside. Tighten gear box
cap screws (23) evenly. Fill with correct grade of
oil until oil flows out through oil level hole.
Grease drive and bearings. (See Lubrication.)
18. Reinstall coupling or belt sheave making sure
that they have a slight slide fit with the shaft and
could be installed by hand.
Where repairs involve parts replacement, it is
recommended that Factory Parts be used to insure fit
and suitability. Delay in making such repairs can be
reduced by having spare parts on hand.
When ordering parts, please furnish all information from
the blower nameplate.
Repairs or adjustments to blowers should be
performed by personnel with a good back ground of
general mechanical experience and the ability to follow
the detailed instructions in this manual. No special tools
are required. Some operations involve extra care and a
degree of precision work. This is especially true in timing
impellers. and in handling bearings. Experience
indicates that a high percentage of bearing failures is
caused by dirt contamination before or during assembly.
Therefore, clean the work area before starting
disassembly. and protect new or reusable parts during
progress of the work. (See page 23 for Repair Kit
Information.)
INTERNAL CLEARANCES
References to operating clearances in this
manual include only one mention of the specific amount
of clearance to be used or expected.
For units in good
condition this information is not essential in field service
work. Situations may arise, however, when it is desirable
to compare existing clearances with the correct
Engineering values or to reestablish clearances.
Listed in Table 6 are the ranges of impeller
clearances used in factory assembly of normal
UNIVERSAL RAI® blowers. It should be kept in mind
that clearances may change slightly in service, but
should never be less than the minimum values listed.
Only well qualified personnel should attempt to measure
clearances for direct comparison with this data.
page 3 - 812
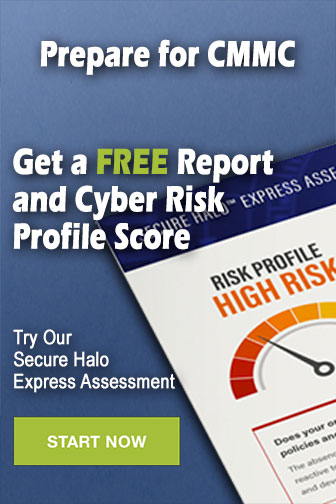