TM 5-3895-374-24-2
INSTALLATION (Continued)
Excessive torque applied to units
may change temperature settings.
Table 1
THERMOSWITCH Controller
Max. Torque
35 ft-lb.*
Standard (5/8 in dia)
(47.5 Nm)
Heavy Duty (13/16 in dia)
70 ft-lb.**
94.9 Nm)
*4 ft-lb. (5.4 N-m) when Teflon tape lubricant is used.
**8 ft-lb. (10.8 N-m) when Teflon tape lubricant is used.
Circular Flange (Style 5) - Three holes in flange allow
easy mounting on any flat surface.
Tension Operated Controllers
Tension operated THERMOSWITCH controllers are
identified by having a number other than 2 or 7 as the
fourth digit of their Catalog Number. Applying excess
tension on the element of a tension operated controller
may permanently warp the element, and in extreme
cases, tear the anchor pin loose. To avoid over-tension,
pay close attention to the following cautions:
1.
Do not expose controller to temperatures above its
upper range limit.
2.
Do not expose controller to more than 100F° (55C°)
above its calibration point. Therefore, preset
controller
to
approximate
required
elevated
temperature before inserting it into the process.
Preset by turning adjusting sleeve in direction of
arrow on head of controller. See Table 3.
3.
If necessary to decrease temperature of a tension
operated controller in a heated system, it may be
necessary to do this in several increments. Do not
turn adjusting sleeve to achieve more than 100F°
(55°C) temperature drop at a time. Wait until
controller stabilizes (begins to cycle). Then repeat
until desired setting is reached.
Compression Operated Controllers
Compression operated THERMOSWITCH controllers
are identified by having a 2 or 7 as the fourth digit of their
Catalog Number. Applying excess compression on the
element of a compression operated controller may result
in warping or crushing it. To avoid over-compression,
pay close attention to the following cautions:
1.
When rotating adjusting sleeve, do not exceed upper
range limit of controller.
2.
When removing controller from a heated system,
never plunge it into a colder medium or use an air
blast for rapid cooling.
Tension or Compression Operated Controllers
1.
Certain gases or liquids (including water at elevated
temperature) could be corrosive and/or cause
electrolytic action which could severely shorten life
of controller. Rate of corrosion or electrolysis is
influenced by many system parameters such as
chemical makeup, temperature of solution, stray
electrical currents, etc. Consult supplier of your
chemicals or Fenwal for application suggestions.
Also, note that Fenwal offers various platings and
Type
321
Stainless
steel,
heliarc
welded
thermowells for added protection.
2.
Be sure that there is sufficient but not excessive
room for the installed controller to expand in
diameter and length.
3.
Insulate head of controller when large ambient
temperature variations may occur. This precaution
is not necessary on junction box type controllers
(Series 17800).
4.
DO NOT immerse controller into liquids or gases
unless it was specified for that job.
5.
DO NOT seal controller head with silicone
materials.
6.
DO NOT thermally shield controller from medium
being controlled.
7.
DO NOT remove adjusting sleeve or turn it in
farther than necessary for desired operation. This
action may permanently damage controller.
8.
DO NOT oil controller. Oil around adjusting sleeve
will flow inside controller, contaminating contacts.
9.
DO NOT handle unit with pliers or force it into
position either by hand or with tools.
10.
DO NOT subject shell of controller to deformation.
WIRING
Connect controller leads in series with the load and power
supply.
DO NOT exceed the ratings indicated on the controller shell.
Capacitors are not required under average conditions.
However, for smoother control at small loads or to prevent
contact bounce due to vibration, the capacitance listed in
Table 2 is recommended. Wire capacitors in parallel with
controller lead connections. Use capacitors rated for a
minimum of 600 VDC with 120 VAC circuits and a minimum
of 1000 VDC for 240 VAC circuits.
page 3 - 1150
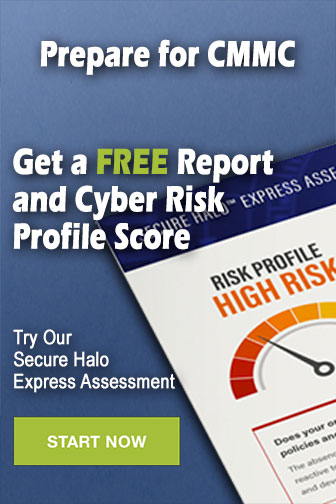