TM 5-3895-374-24-2
B: Breather; D: Drain; L: Oil Level Pug; P: Plug
Fig. 2-Mounting Positions.
Note: If motor mount, motor and sheaves are to
be installed on reducer before mounting screw
conveyor drive to trough end, bypass step 2;
perform steps 3 and 4, and then return to step 2.
2.
On sizes SCXT3A, SCXT4A, and SCXT5B, use
lifting tab to hoist the screw conveyor drive into
position. Slide shaft into screw and adapter over
trough end studs. Only one set of adapter holes will
fit over trough end studs. If the mounted position of
the screw conveyor drive varies by 15° from any of
the four horizontal mounting positions in Fig. 2, an
incorrect set of holes has been selected for coupling
adapter to reducer. This can be corrected by
removing adapter screws and rotating reducer to its
proper position. Reinstall and tighten adapter
screws to torque specified in Table 4 on page 8.
Install lockwashers and tighten nuts on trough end
studs. Attach drive shaft to screw.
3.
Remove the three bolts from reducer housing
required for mounting the SCD Motor Mount. Place
the motor mount in position and install the three
housing bolts supplied with the motor mount.
Tighten bolts to torque specified in Table 4 on page
8.
4.
Install motor, drive sheave and driven sheave so that
driven sheave is as close to the reducer housing as
practical. Install V-belt and tension with the four
adjusting screws provided on the SCD Motor Mount.
Install belt guard. Make required electrical
connections for motor.
DANGER
The user is responsible for conforming
with the National Electrical Code and all
other applicable local codes. Wiring
practices, grounding, disconnects and
overcurrent protection are of particular
importance. Failure to observe these
precautions could result in severe bodily
injury or loss of life.
5.
Because reducer is shipped without oil, it is necessary to
add the proper amount before operating the drive. Use a
high grade petroleum base, rust and oxidation inhibited (R
& O) gear oil-see lubrication tables.
CAUTION
Unit is shipped without oil. Add proper
amount of recommended lubricant before
operating. Failure to observe these
precautions could result in damage to, or
destruction of, the equipment.
6.
Retighten bolts and pipe plugs after a few days operation.
This prevents oil leakage.
LUBRICATION
Under average industrial operating conditions, the
lubricant should be changed every 2500 hours of
operation or every 6 months, whichever occurs first.
Drain reducer and flush with kerosene, clean magnetic
drain plug and refill to proper level with new lubricant.
CAUTION
Too much oil will cause overheating
and too little will result in gear failure.
Check oil level regularly.
CAUTION
Extreme pressure (EP) lubricants are
not
recommended
for
average
operating conditions. Failure to
observe
these
precautions
could
result in damage to, or destruction of,
the equipment.
Under extreme operating conditions, such as rapid rise
and fall of temperatures, dust, dirt, chemical particles,
chemical fumes, or oil sump temperatures above 2000F, the
oil should be changed every 1 to 3 months depending on
severity of conditions.
CAUTION
Do not use oils containing slippery
additives
such
as
graphite
or
molybdenum disulfide in the reducer
when backstop is used. These additives
will destroy sprag action. Failure to
observe these precautions could result in
damage
to,
or
destruction
of,
the
equipment.
page 3-790
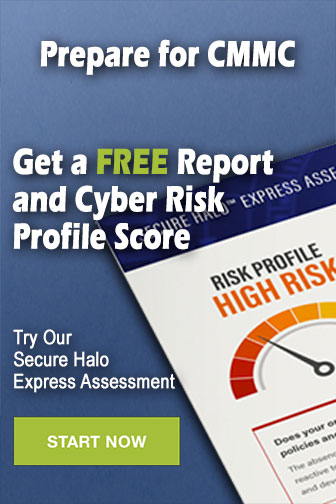