TM 5-3895-374-24-1
GP440FG
5.
The piping from the gas regulator outlet to the burner gas manifold should be sized to minimize pressure losses.
6.
Check blower rotation. The impeller should rotate toward the blower discharge.
7.
Inspect and operate the plant exhaust damper and control. This damper system should be capable of maintaining
a consistently negative drum (front) pressure of 0.2 to 0.5 inches wc from low to high firing rates.
8.
Install a gas sampling probe in the dryer rear plate. (See Application Sheet GJ73.)
9.
Set the low gas pressure switch to an initial setting of ½ psig.
10.
Set the high gas pressure switch to an initial setting of 5 psig.
11.
Complete the initial adjustment of the gas butterfly as follows: The valve is factory set to travel 90 degrees from
position 1 to position Run. This travel can be modified to increase or decrease low fire by choosing a lower or
higher starting point.
12.
Open all shutoff cocks in the gas line upstream of the gas pressure switch.
13.
Start gas flow to the gas manifold.
14.
Adjust the gas regulator until the pressure gauge upstream of the automatic blocking valve indicates a pressure of
2 psig.
15.
High fire can be modified by increasing or decreasing gas pressure. After setting high fire gas pressure, low fire
must be rechecked. Refer to individual Burner Performance Tables for gas flows thru the gas orifice meter.
16.
Burner flame adjustment spin vanes can be set at 35 to 60 degrees. Thirty-five narrows the flame. Sixty degrees
widens the flame. Forty-five degrees is a nominal starting point.
17.
Burner air adjustments: (See Section C - Operation)
18.
Recheck all linkages for tightness.
19.
Install a manometer (U-tube) across the gas orifice meter taps.
20.
Connect a flue gas analyzer to the gas sampling probe.
21.
Flue gas readings should be taken with the burner firing at operating tonnage. (See Application Sheet GJ73)
(page 3-510)
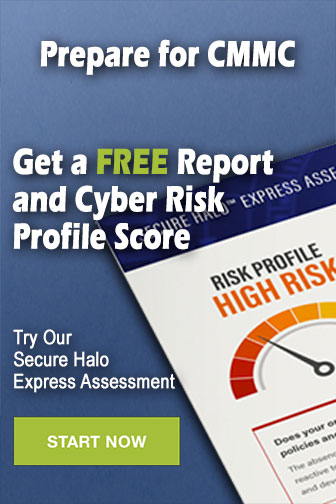