TM 5-3895-374-24-2
VIKING PUMPS
DISASSEMBLY CONTINUED
(3) Remove the idler and bushing assembly from the pin. Inspect
for signs of excessive pin, head, idler and/or bushing wear.
Replace any worn parts.
Note the pin grease groove position, if applicable, prior to re-
moving.
(4) Loosen the set screws holding the bearing to the shaft. Re-
move the cap screws that secure the casing and bracket as-
sembly. The casing, with the rotor and shaft assembly, can
be removed from the bracket.
(5) Loosen the packing gland nuts. Note. with mechanical seal
pumps, remove the seal seat retainer which exposes the
seal. Carefully remove the mechanical seal. Remove the seal
cavity plug and loosen the setscrews securing the set
collar to the shaft. Remove the set collar. Inspect the seal for
signs of wear and/or scouring.
(6) Carefully remove the rotor and shaft from the pump. Once re-
moved inspect for signs of excessive scouring and/or wear
Replace if required.
(7) Inspect the casing bushing for signs of excessive wear. If it
must be replaced It can be pressed out through the stuffing
box.
(8) The bearing can be removed from the bracket by removing
the capscrews and aluminum retainer. Inspect for damage
and replace If necessary.
(9) All parts can be inspected again for wear. scouring and/or
damage before the pump is reassembled
REASSEMBLY
NOTE:
Should it be necessary to install new carbon bushings,
extreme care should be taken to prevent the bushings
from fracturing. It is a brittle material and easily cracked.
If cracked, these bushings will quickly disintegrate. An
arbor press should be used to install carbon bushings. Be
sure the bushing is started straight and do not stop the
pressing operation until the bushing is in the proper posi-
tion. Starting and stopping this operation invariably re-
sults in bearing failure.
Carbon bushings for high temperature systems are sup-
plied with extra interference fits and must be installed by
an arbor press after heating the bearing bracket or idler
to 450°F. Check the bushing for cracks after installation.
(1) Press the casing bushing into place and check the after press
fit value to ensure .002 inches minimum running clearance
exists between the bushing and shaft. Lubricate prior to star-
tup.
(2) Remove all burrs and rough surfaces from the rotor and shaft
and assemble in the casing. Start the shaft through the cas-
ing bushing and slowly, turning the rotor, push it into the cas-
ing as far as it will go.
(3) Place the head gaskets on the head. The proper amount of
gaskets should be used to provide the necessary end clear-
ance within the pump so it turns freely with no appreciable
end play.
(4) Press the idler bushing into the idler and ensure .002 inches
minimum running clearance exists between the bushing and
pin. Replace the idler disc if one was originally supplied. En-
sure this area is lubricated prior to startup.
(5) Replace the idler pin at this time by pressing the old one out.
The new pin can be inserted but check the pin bore condition
as a liquid sealant may be required if scouring is present. En-
sure the pin is below the highest point on the head crescent
after insertion. Put the Idler on the head and ensure it rotates
freely.
(6) The head can now be assembled on the pump. Tilt the top of
the head away from the pump slightly until the crescent en-
ters the inside diameter of the rotor and rotate the idler until
Its teeth mesh with the rotor teeth Do not damage the head
gaskets. Check that the head and casing position markings
are aligned. Tighten the head capscrews or nuts evenly and
then check the end clearance. If the pump shaft cannot be
rotated, more gaskets must be added. If, however, the pump
has any noticeable end play, remove enough gaskets so the
pump has no appreciable end play but still turns freely.
(7) Pack the pump. It is good practice to install a set of new pack-
ing. A packing suitable for the liquid being pumped should be
used. If the pump has a lantern ring it must be located below
the grease fitting or flushing connection. The grease fitting
may be removed to facilitate positioning of the lantern ring.
Cut the packing into individual rings that wrap exactly around
the shaft. Install and seat each ring one at a time, staggering
the ring joints from one side of the shaft to the other. Lubri-
cate the packing rings with oil, grease or graphite to aid in as-
sembly. A length of pipe or tubing will help in seating the
packing rings. When installing the gland it must enter the
stuffing box at least one-eighth of an inch tightening the pack-
ing gland nuts
(8) Install the mechanical seal: Place the setcollar on the shaft
and tighten the setscrew through the connection provided.
The seal is simple to install and good performance will result
if care is taken In its installation. (Never touch the sealing
faces with anything except the fingers or a clean cloth)
Spread a film of lubricating oil on the inside diameter of the
synthetic rubber bellows. Check the end of the pump shaft
for sharp burrs or edges which might cut the bellows. Slide
the seal rotary member over the shaft and up against the
spring. (The spring washer and spring must be put on the
shaft first and in that order). Coat the synthetic rubber seal
seat retainer with lubricating oil and push the seal seat into
the ending cap. Put the end cap gasket on the end of the cas-
ing. Slide end cap over the shaft and flush both the seal seat
and carbon wear ring in the seal rotary member with oil. Push
the end cap up until the mating surfaces of the seal meet. In-
stall the capscrews then tighten evenly.
(9) Replace the ball bearing if necessary and reassemble into the
bracket. Tighten the capscrews to secure the bearing re-
tainer. Place the shaft through the bearing and locate the
bracket onto the casing. Tighten the capscrews securing the
casing and bracket. Ensure that the assembled unit rotates
freely then secure the bearing setscrews. Failure to tighten
these setscrews will result In rapid pump wear.
NOTE: The after press fit value is the final size for carbon bush-
ings. No sizing should be required.
(page 3 - 897)
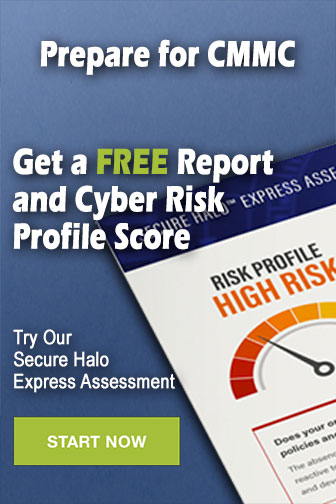