TM 5-3895-374-24-1
OVERVIEW
BASIC AIR COMPRESSOR COMPONENTS
The basic components of the air compressor are the
electric motor, pump, and receiver The receivers may be
vertical or horizontal, varying In size and capacity See
Fig 1.
Electric Motor
The electric motor powers the compressor pump The
motor drives a pulley and two belts, which transfer power
from the motor to the pump pistons via a flywheel and a
crankshaft The flywheel fan helps cool the compressor
pump.
IMPORTANT: These compressors require installation
of a magnetic starter, to prevent motor damage in
the event of a thermal overload. Failure to Install a
magnetic starter will void the manufacturers warranty
See page 9 for further Information on magnetic starter
installation and wiring (Some units are supplied with a
factory-installed magnetic starter ).
Compressor Pump
The pump compresses the air and discharges it Into the
receiver. Two-stage air compressors have a minimum of
two pump cylinders. By compressing the air twice, first In
a larger, low pressure cylinder, then in a smaller, high
pressure cylinder, two-stage compressors can produce
pressures from 145-175 psi.
As the piston in the pump cylinder moves downward, air
enters the large cylinder through the filter and air Intake
valves at atmospheric pressure.
On the upstroke, the piston in the large cylinder
compresses the air to approximately 50 psi, and
discharges It to the smaller cylinder through the
intercooler tube. The air is cooled by the flywheel fan as
It passes through the intercooler and into the smaller
cylinder.
In the smaller cylinder, the air is compressed to its final
pressure. As the piston moves upward, it compresses
the air and discharges It into the receiver through a
check valve.
Receiver
The receiver (tank) stores the compressed air A check
valve at the receiver inlet prevents the compressed air in
the receiver from flowing back Into the compressor
pump.
Pressure Switch
When the air pressure in the receiver reaches the
factory-set limit, the pressure switch shuts down the
motor. As compressed air Is used and the pressure level
in the tank drops to a pre-set level, the pressure switch
restarts the motor and the compressor resumes pumping
air.
TYPICAL INSTALLATION
Fig 2 Illustrates a typical Installation of an electric two-
stage air compressor
Air Dryers and Aftercoolers
Two types of aftercoolers are available The type shown
In Fig 2 is Installed directly in the air line It both cools and
dries the air.
Another type mounts directly on the belt guard of the
compressor It functions like a radiator, using fan-driven
air to cool the compressed air before it enters the
receiver.
Moisture Removal and Air Filtration
As the air cools, moisture will condense in the lines This
moisture must be removed before it reaches the tool. To
remove this moisture, run the main air line downhill to a
trap and drain, as specified in Fig 2 Air/water filters
should also be Installed In the positions shown.
Air Pressure Regulation
The air pressure gauge on the pressure switch
measures air pressure inside the receiver, not
pressure in the airline. Install an air regulator in the drop
line for each tool, to regulate air pressure to that tool.
Never exceed the maximum pressure rating of the
tool.
Air Lubrication
Install an air lubricator only for those tools requiring
lubrication. Do not use a lubricator for paint spraying
or similar applications. The oil will contaminate the
paint and ruin the job.
Shut-Off Valves
Install shut-off valves in each drop line, to isolate the tool
and Its accessories for servicing You can also Install a
bypass line around an accessory, as shown in Fig 2.
WARRANTY/REGISTRATION CARD
Please fill out the enclosed warranty/registration card
and mail it to the factory.
200-2009
(page 3-628)
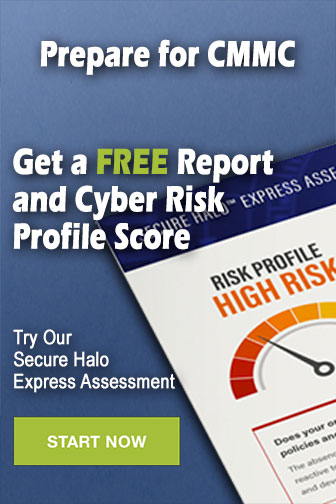