TM 5-3895-374-24-1
Sure-Flex Installation Instructions (continued)
Different coupling sleeves require different degrees of alignment precision. Locate the alignment values for your sleeve
size and type in Table 2 below.
5
Check
parallel
alignment
by
placing
a
straightedge across the two coupling flanges and
measuring the maximum offset at various points around
the periphery of the coupling without rotating the coupling
If the maximum offset exceeds the figure shown under
"Parallel" in Table 2, realign the shafts.
6
Check angular alignment with a micrometer or
caliper. Measure from the outside of one flange to the
outside of the other at intervals around the periphery of
the coupling. Determine the maximum and minimum
dimensions without rotating the coupling. The difference
between the maximum and minimum must not exceed
the figure given under "Angular" in Table 2. If a
correction is necessary, be sure to recheck the parallel
alignment
TABLE 2-MAXIMUM RPM AND ALLOWABLE MISALIGNMENT
(Dimensions in inches)
Note Values shown above apply if the actual torque transmitted is more than 1/4 the coupling rating For lesser torque,
reduce the above values by ½.
*Type H and HS sleeves should not be used as direct replacements for EPDM or Neoprene sleeves.
(1) Value when using 6J flanges is 2 125
7 If the coupling employs the two-piece sleeve with the wire ring, force the ring into its groove in the center of the
sleeve. It may be necessary to pry the ring Into position with a blunt screwdriver.
8 Install coupling guards per OSHA requirements.
CAUTION: Coupling sleeves may be thrown from the coupling assembly with substantial force when the coupling Is
subjected to a severe shock load or abuse.
T. B. WOOD'S SONS COMPANY a Chambersburg, PA 17201
T. B. WOOD'S CANADA LTD. - Stratford, Ontario N5A 6V6
FORM 741E 5-92
Printed In U S A.
(page 3-572)
Angular
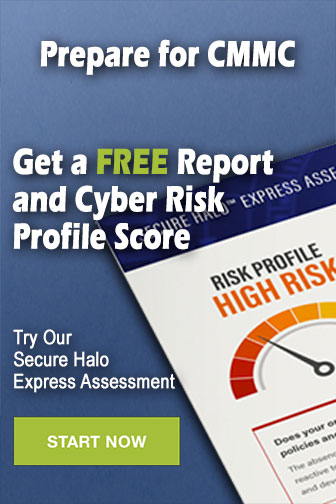