TM 5-3895-374-24-1
Disassembling Gear Reducers
General
The following information is a general guide-line for the
disassembly of a typical EURODRIVE reducer. If additional
information is needed, call our office and have the information
contained on the reducers nameplate available.
On the reducers nameplate, under "Type, a code of several
digits will be embossed. The first digit (either an R, S, K, or F)
establishes the type of reducer
Typical cross sections of the four EURODRIVE reducer types
are shown on page 20
Some types and sizes are quite different than the ones shown
on page 20 For this reason, a Spare Part List should be
obtained for proper identification of parts prior to disassembly
The Spare Part Lists do not bear any part numbers for the
gears, since these will vary for different ratios EURODRIVE
gears have embossed numbers for positive identification.
When ordering replacement gears, please have this number
ready.
Certain
reducer
parts
will
be
destroyed
during
the
disassembling process Replacement parts should be on hand
before starting the disassembly These items generally include
gaskets, seal rings, bearing caps, nilos rings and oil slingers.
A set of shims is needed if gears are to be replaced.
Bearings used are standard sizes, their international code is
shown on our Spare Parts Lists.
Helical Reducers Type R...","F..."
Drain oil and remove input and output cover assemblies. RX "
and FA.." type reducers do not have any output covers The
FA " reducer has a square coverplate instead.
All shafts, gears and bearings can be removed from the main
body of the reducer after the circlips are removed.
Some shafts have to be pressed out of the gearhubs. To do
so, on some gears supports have to be placed between the
gears and the casting, to keep the gears aligned in a
horizontal position during the pressing action
Assemble the reducer in reverse order, placing shims between
bearings and circlips to eliminate endplay.
If the input pinion has been removed from its shaft (motor shaft
or input shaft) the shaft and the pinion have to be cleaned of
any grease Apply a few drops of "Loctite RC/609" on the shaft
before remounting the pre-heated pinion gear
On the assembled reducer, with the cover(s) removed, the
embossed identification numbers should be visible on the
gears.
Gaskets should be set in liquid seal (Permatex) to ensure
tightness. Reducers of the latest design (R .2,3, K .6) have no
gaskets on the output housings or bearing flanges Loctite
574 has to be applied in all areas.
Worm Gear Reducers Type "S.."
Proceed as with type "R - and "F " reducers, with following
additional considerations:
On "S " type reducers, footmounted style, the output shaft
must be removed to enable the
removal of the remaining gears.
Removal of the output shaft:
After the seals, circlips, shims and bearing caps are removed,
the gearbox must be placed under a press, with the output
shaft pointing downwards Place keystock of appropriate
dimensions inside the reducer, below the wormwheel, to keep
the shaft/wormwheel assembly in the centre of the reducer,
while the shaft is being pressed out Failure to support the
worm wheel may damage the worm gear.
On flange-mounted and hollow shaft reducers type ·SF " and
'SA " these procedures are not needed, since the output shaft
can be taken out of the housing together with the worm wheel.
Worm gear adjustment:
The worm wheel has to be centred on top of the worm gear,
when assembling the drive in order to ensure proper
lubrication, and achievement of full nominal service life of the
gears.
For this purpose, shims are provided on both sides of the
worm wheel bearings Fig 7 The location of the contact area
between worm gear and worm wheel bearings.
Fig.7: The location of the contact area between worm gear and
worm wheel.
Proper shimming can be checked by applying a thin coat of
dark grease (Molykote) onto the worm wheel and running the
greased portion several times through the gear mesh. The
gear contact will leave an imprint on the grease film. This
imprint should be centred at the middle of the worm wheel, or
slightly offset in the direction of the worm gears rotation. See
Fig.7 This offset will ensure better oil penetration into the gear
mesh.
Bevel Gear Reducers Type "K ..."
There are special instructions available for the disassembly
and assembly of these reducers Please call our office for more
information.
(page 3-616)
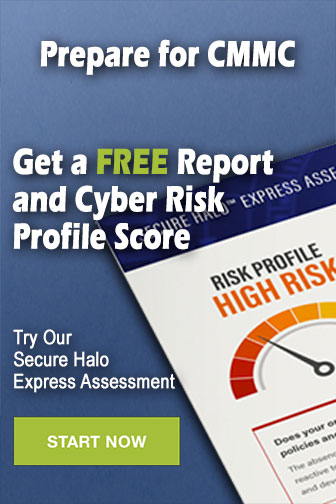