TM 5-3895-374-24-1
Bulletin No. 30072-013-01
January, 1992
Overload Relays ?
Terminals ?
Inspecting and
Replacing Contacts
Manual Operation
Coil Replacement
Table 1
Field Modification Kits
Kit
Class 9999 Type
Factory Modifications
(Form)
Push button, start-stop
SA2
A
Push button, on-off
SA10
A3
Selector switch, hand-off-auto
SC2
C
Selector switch. on-off
SC22
C6
Red pilot light (slip-on enclosure)
SP4R
P1
Red pilot light (hinged door enclosure)
SP14R
P1
A melting alloy overload relay is supplied as standard with provisions for one or three
thermal units. The contact unit (item 7) of the melting alloy overload relay is available with a
normally-open or normally-closed isolated alarm contact in addition to the standard
normally-closed contact. The contact unit with alarm circuit contacts can be installed in the
field (refer to Table 5).
Non-temperature compensated bimetallic overload relays are available as an optional
feature (Form B5). Ambient-temperature compensated bimetallic overload relays are also
available as an optional feature (Form Y59). Bimetallic overload relays have provisions for
one or three thermal units.
These overload relays are not designed for field repair and should not be disassembled.
Use copper wire only on standard device power and control terminals. Box lugs are suitable
for wire sizes #14-1/0 kcmil. Pressure ,wire control terminals are suitable for wire sizes
#16-12, solid or stranded.
Contacts are not harmed by discoloration and slight pitting. Do not file contacts, as it
wastes contact material. Replacement is only necessary when the contact has worn thin.
Replacement contacts for starters or contactors are available as kits Order from Table 5.
It is unnecessary to remove any wiring to visually inspect the contacts. To inspect, loosen
the four screws (item D) holding the contact actuator to the contact block. Lift the contact
actuator to expose the contacts.
WARNING
HAZARDOUS VOLTAGE.
Disconnect all power before manually operating equipment.
Manual operation with power on can cause contact arcing and unexpected
energization of load, resulting in personal injury or equipment damage.
Manual operation of contactors and starters may be accomplished by pushing the contact
carrier down with a screwdriver. There is a step on the outside of the contact carrier
suitable for this use.
To remove the coil, loosen the two captive cover screws (item A). Disconnect wires from
the coil terminals and remove the cover. Loosen the two screws (item B) holding the
magnet in place. Remove the coil and magnet. Manually operate the contact carrier and
remove the armature. Separate the coil from the magnet.
To replace the coil, first assemble the magnet, coil and armature and insert the complete
unit. Approximately 3/8 of an inch space should exist between the top outside surface of
the coil and inside surface of the magnet. If this space does not exist and magnet tends to
© 1992 Square D All Rights Reserved
?Revised 1/92
(page 3-113)
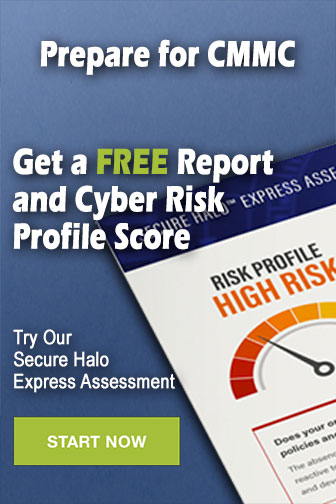